PRODUCTS DETAILS
Spiral Welded Pipe
Spiral welded pipes, also known as helical welded pipes, are steel pipes manufactured using a continuous welding process where a steel coil is shaped into a spiral and welded along the seam. These pipes are widely used in high-pressure, large-diameter, and long-distance pipeline applications. The spiral welding technique provides excellent strength, flexibility, and cost efficiency, making it suitable for industries such as oil & gas, water distribution, structural engineering, and dredging.
Spiral welded pipes are often preferred over longitudinal welded pipes due to their ability to handle high pressure and their efficient production method. They are typically made from carbon steel, stainless steel, or alloy steel, depending on the application requirements.
Spiral welded pipes offer a strong, cost-effective, and versatile solution for transporting liquids, gases, and structural applications.
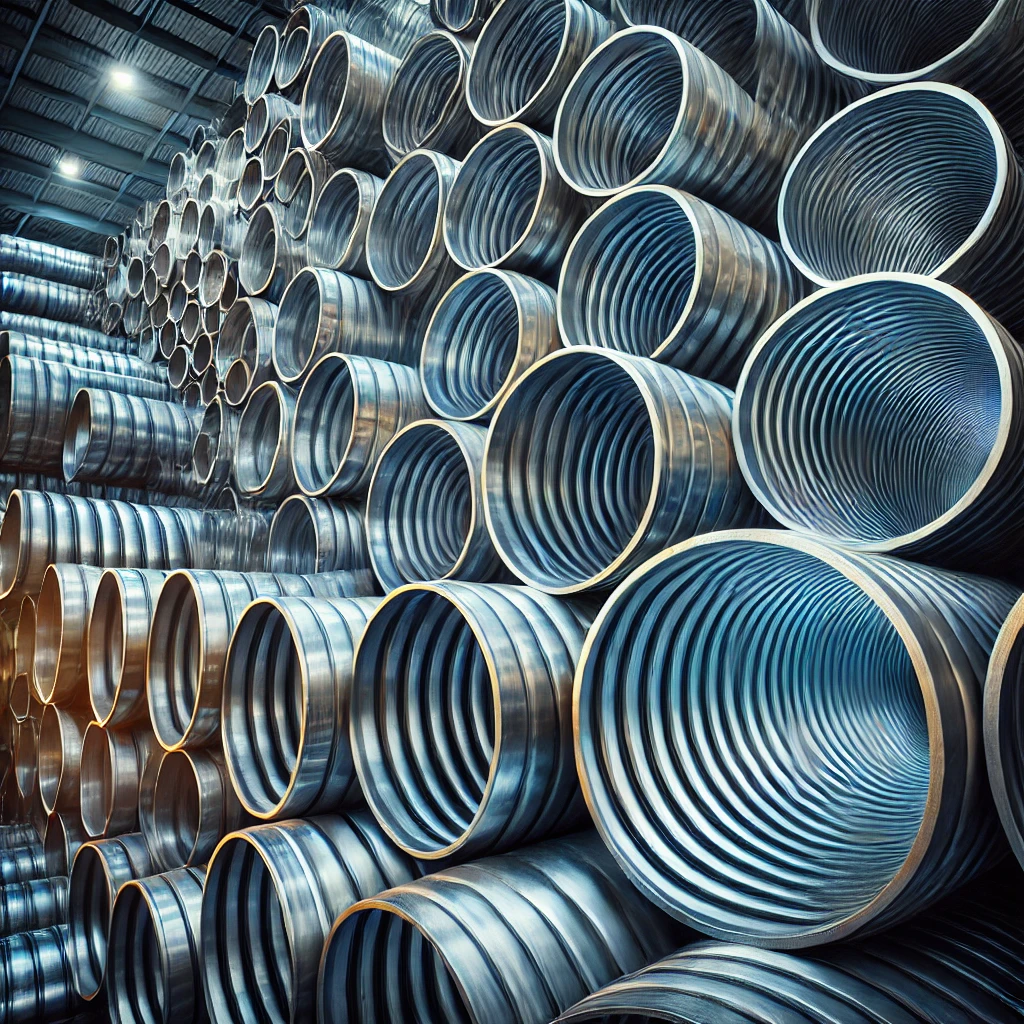
DESCRIPTION EVENT
Manufacturing Process of Spiral Welded Pipes
- Coil Unwinding: A continuous steel strip is fed into the forming machine.
- Spiral Forming: The strip is shaped into a cylindrical pipe by bending it in a helical pattern.
- Welding: The edges of the spiral are continuously welded using submerged arc welding (SAW) for strong, durable joints.
- Inspection & Testing: The pipes undergo ultrasonic, radiographic, and hydrostatic tests to ensure quality.
- Cutting & Finishing: The pipes are cut to the required length and undergo surface treatment, such as galvanization or coating, for corrosion resistance.
Properties of Spiral Welded Pipes
- High Strength: The helical weld design distributes stress evenly, enhancing durability.
- Cost-Effective: More economical than seamless or longitudinal welded pipes for large diameters.
- Large Diameter Production: Suitable for manufacturing pipes with a very large diameter.
- Flexibility: The spiral welding process allows for easy customization of length and thickness.
- Smooth Flow Characteristics: The uniform internal surface minimizes friction and improves fluid transportation.
- Corrosion Resistance: Can be coated or galvanized to improve resistance to rust and chemicals.
Types of Spiral Welded Pipes
- Carbon Steel Spiral Welded Pipes: Used in general construction, water supply, and oil pipelines.
- Stainless Steel Spiral Welded Pipes: High corrosion resistance, used in marine, chemical, and food processing industries.
- Galvanized Spiral Welded Pipes: Zinc-coated for enhanced durability in outdoor and underground applications.
- Coated Spiral Welded Pipes: Additional coatings such as epoxy or polyethylene for improved corrosion resistance in buried pipelines.
Applications of Spiral Welded Pipes
Due to their strength and versatility, spiral welded pipes are widely used in various industries:
- Oil & Gas Pipelines: Used for transporting crude oil, natural gas, and petroleum products over long distances.
- Water Supply & Irrigation: Ideal for large-scale municipal and industrial water transportation.
- Dredging & Marine Applications: Used in harbor, canal, and river dredging projects.
- Structural & Construction Industry: Used for bridges, buildings, stadiums, and piling foundations.
- Hydropower & Energy Sector: Used in hydroelectric plants and power stations for water transport.
- Firefighting Systems: Used in firewater distribution networks in industrial plants.
Advantages:
- High Load-Bearing Capacity: Suitable for high-pressure and heavy-duty applications.
- Efficient & Continuous Production: Faster manufacturing process compared to longitudinal welded pipes.
- Cost-Effective for Large Projects: More economical than seamless pipes for large-diameter applications.
- Versatile Applications: Used in oil, gas, water, and structural projects.
GRADE | T.S. (min) | Y.S. (min) | Elongation | O.D. | +/-0.5 mm | ||
GRADE | Mpa | Mpa | 25.4 mm & under | Over 25.4 mm | Thickness | +/-10% | |
YST-210 YST-240 YST-310 | 330 410 450 | 210 240 310 | 12 10 8 | 20 15 10 | Weight | ||
(1) Single Pipe | 0.02 | ||||||
(2) On lots of 10 Tonne | 7.50% |
FOLLOW US
…
- Telegram
- Youtube