PRODUCTS DETAILS
ERW Pipes
Electric Resistance Welded (ERW) pipes are steel pipes manufactured using a high-frequency electrical current to heat and fuse the edges of a steel strip, forming a continuous welded seam. These pipes are widely used in industries such as oil & gas, construction, water distribution, and automotive manufacturing due to their high strength, cost-effectiveness, and uniformity in size and shape.
ERW pipes are available in different materials, including carbon steel, stainless steel, and galvanized steel, making them suitable for a wide range of applications. Their smooth internal surface ensures efficient fluid and gas transportation, while their strong welds provide excellent mechanical properties.
ERW pipes provide a cost-effective and efficient solution for transporting fluids, gases, and structural applications.
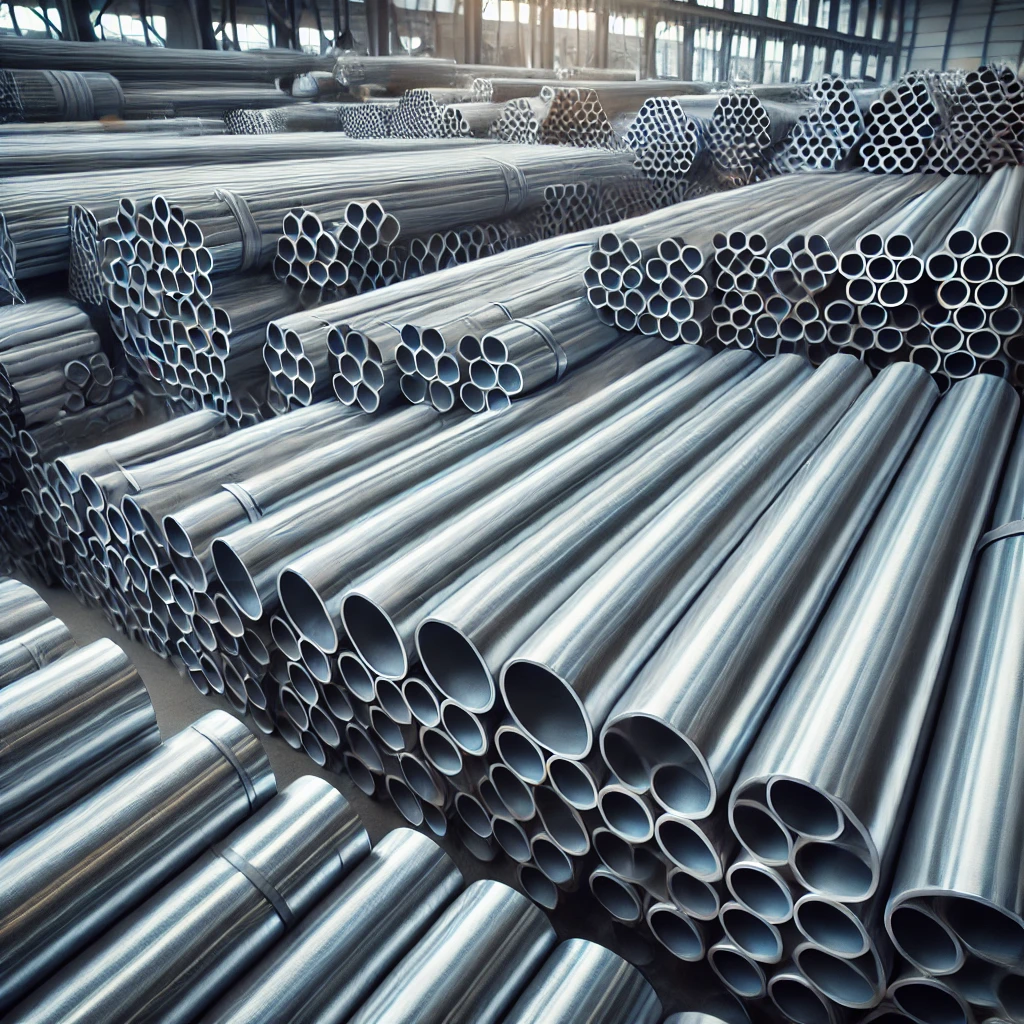
Manufacturing Process of ERW Pipes
- Steel Coil Preparation: A flat steel strip (hot-rolled or cold-rolled) is cut and fed into the forming machine.
- Pipe Forming: The strip is gradually shaped into a cylindrical form using rollers.
- Electric Resistance Welding: High-frequency electric current is applied to the edges, heating and fusing them to form a continuous seam.
- Seam Inspection & Testing: The weld is inspected for defects using non-destructive testing methods like ultrasonic or X-ray inspection.
- Sizing & Cutting: The welded pipe is sized to precise dimensions and cut into required lengths.
- Surface Treatment: The pipe may undergo galvanization, coating, or polishing for added durability and corrosion resistance.
Properties of ERW Pipes
- High Dimensional Accuracy: Manufactured with precise control over diameter, wall thickness, and length.
- Smooth Inner & Outer Surface: Ensures efficient fluid flow and reduces resistance.
- Good Mechanical Strength: Can handle moderate pressure and mechanical stress.
- Corrosion Resistance: Can be galvanized or coated for protection against rust.
- Cost-Effective & Mass-Produced: Suitable for large-scale industrial applications.
- Lightweight Compared to Seamless Pipes: Easier to transport and install.
Advantages:
- Uniform Wall Thickness: Provides consistent strength and durability.
-
High Production Efficiency: Faster and more economical than seamless pipes.
- Strong Weld Integrity: Modern welding techniques ensure high-quality joints
- Available in Various Grades: Suitable for different industries and applications.
Wall Thickness | NominalBore 7" NB 193.7 mm OD | NominalBore 8" NB 219.1 mm OD | NominalBore 10" NB 273 mm OD | NominalBore 12" NB 323.7 mm OD | NominalBore 14" NB 355.6 mm OD | NominalBore 16" NB 406.4 mm OD | NominalBore 18" NB 457mm OD | NominalBore 20" NB 508 mm OD |
mm | Kg/mtr | Kg/mtr | Kg/mtr | Kg/mtr | Kg/mtr | Kg/mtr | Kg/mtr | Kg/mtr |
4.85 | 22.59 | 25.62 | 32.07 | 38.13 | - | - | - | - |
5.2 | 24.17 | 27.43 | 34.34 | 40.85 | - | - | - | - |
5.6 | 26 | 29.28 | 36.93 | 43.93 | 48.11 | - | - | |
6 | 27.88 | 31.53 | 39.5 | 47.02 | 51.49 | 61 | 69 | - |
6.35 | 29.34 | 33.28 | 41.73 | 49.67 | 54.43 | 62.35 | 70.5 | 78.5 |
7.01 | 32.77 | 36.76 | 46.43 | 55.45 | 61.82 | 69.04 | - | - |
7.94 | - | 41 | 50.95 | 61.85 | 67.98 | 77.94 | 87.8 | - |
8.18 | - | 42.56 | 53.42 | 65.12 | - | - | - | - |
9.53 | - | 51.5 | 60.24 | 73.75 | 81.21 | 93.13 | 105 | 117 |
12.7 | - | - | - | - | 107.28 | 123.3 | 139 | 155 |
(a) Thickness | ||
-1 | Butt welded Light tubes | +Not limited- 8 percent |
+ Not Limited - 10 percent | ||
-2 | Seamless Tubes | +Not Limited- 12.5 percent |
(b) Weight : | ||
-1 | Single tube (light series) | +10 percent- 8 percent |
-2 | Single tube(medium & heavy Series) | +10 percent |
Tolerance on Thickness and Weight : as per IS 1239 The following manufacturing tolerance shall be permitted on the tubes and sockets. | MAXIMUM PERMISSIBLE PRESSURE AND TEMPERATE FOR TUBES WITH STEEL COUPLINGS OR SCREWED AND SOCKETED JOINTS | ||||||
Nominal Bore mm | Maximum Permissible Pressure N/mm2 | Nominal Bore mm | Kg./cm2 | Maximum PermissibleTempreature 0C | |||
Up to and Including 25 mm | 1.2 | 12.24 | 260 | ||||
Over 25 mm up to and Including 40 mm | 1.03 | 10.5 | 260 | ||||
Over 40 mm up to and Including 80 mm | 0.86 | 8.77 | 260 | ||||
Over 80 mm up to and Including 100 mm | 0.69 | 7.04 | 260 | ||||
0.83 | 8.77 | 177 | |||||
Over 100 mm up to and Including 125 mm | 0.69 | 7.04 | 171 | ||||
Over 125 mm up to and Including 150 mm | 0.5 | 5.1 | 160 | ||||
For tubes fitted with appropriate flanges of suitably butt welded together,the Max, permissible pressure shall be 21.00 Kg/cm2 and Max. permissible temp. 260 C |
FOLLOW US
…
- Telegram
- Youtube